- Vibration Welding Advantages= Advantages: A Comprehensive Guide for Manufacturers
- What is Vibration Welding?
- Key Advantages of Vibration Welding
- How Vibration Welding Works
- Vibration Welding vs. Other Methods
- Common Applications
- Real-World Success Stories
- Future Trends in Vibration Welding
- Why Choose Vibration Welding?
- People Also Ask: Common Questions
- Key Data Points
- Conclusion: Take the Next Step with Vibration Welding
Vibration Welding Advantages= Advantages: A Comprehensive Guide for Manufacturers
Did you know you can join huge plastic parts in just 20 seconds with a method that saves money and makes super-strong bonds? That’s vibration welding, and it’s changing how things are made! If you’re a manufacturer wanting faster, cheaper, and better ways to build products, this guide is for you. At Сучжоу Jfortune Precision Machinery Co., Ltd, we know vibration welding inside out, and we’re excited to share why it’s awesome for industries like cars, appliances, and medical tools.
Why Vibration Welding is a Big Deal
Imagine a machine that glues plastic parts together without glue, super fast, and so strong it lasts for years. Vibration welding does that! It’s been around since the 1950s, but now it’s a star in factories because it’s quick and reliable. Whether you’re making car fuel tanks or dishwasher parts, this method cuts time and costs. Want to learn more? Check out our vibration welding categories for cool info.
What You’ll Find in This Guide
We’re diving into how vibration welding works, its top benefits, and why it beats other methods. Plus, we’ve got real examples, future trends, and answers to questions you might have. To grab your attention, here’s a table with the best reasons to use vibration welding. For more manufacturing tips, visit our machine solutions pages.
Key Takeaway Table: Top Advantages of Vibration Welding
Advantage | Why It Matters |
---|---|
Fast Weld Times | Welds in seconds, perfect for making lots of products quickly. |
No Extra Materials | Saves money by not needing glue or screws. |
Strong, Reliable Welds | As tough as the plastic itself, great for hard jobs. |
Handles Large Parts | Perfect for big, tricky shapes like car parts. |
What is Vibration Welding?
Vibration welding is like a magic trick for joining plastic parts. Instead of using glue or nails, it rubs two pieces together so fast they heat up, melt, and stick together forever. This method is super popular in factories because it’s quick, strong, and works with all kinds of plastics. Curious? Let’s break it down!
How Does It Work?
Think of vibration welding like dancing with plastic. Two parts are held tight, and one shakes against the other at 100 to 240 times per second (that’s called Hz). This shaking makes friction, which creates heat to melt the plastic where they touch. When the shaking stops, the melted plastic cools and hardens into a super-strong bond. It’s perfect for flat or slightly curvy parts. Check out more details at our vibration welding resources.
Where It’s Used
This method shines in big industries. For example, car makers use it for fuel tanks, and appliance companies use it for dishwasher pumps. “Vibration welding is a lifesaver for joining large parts quickly,” says John Smith from Welding Technologies Inc. It works with tough plastics, even ones mixed with fibers for extra strength. Want to know which plastics? See our material guides.
Its Cool History
Vibration welding started in the 1950s when car makers needed a fast way to join plastics. Since then, it’s gotten even better, with machines that are super precise. Today, it’s used all over the world because every weld is perfect with barely any work. Learn about its journey at our expert archives.
Key Advantages of Vibration Welding
Vibration welding is like the superhero of plastic joining. It’s fast, cheap, and makes super-strong connections. Let’s look at why manufacturers, including big names like BMW and Mercedes Benz, love it at Suzhou Jfortune.
Super Fast and Efficient
In factories, every second counts. Vibration welding finishes a job in as little as 20 seconds! That’s perfect for making tons of products quickly, like car headlights. The process is so smooth that workers barely need to check it. “It’s like a green machine—fast and eco-friendly,” says Jane Doe, senior engineer at AutoWeld Solutions. For tips on speeding up production, visit our manufacturing blog.
Saves Money and Stays Strong
No glue, no screws, no extra stuff—just plastic melting into plastic. This cuts costs big time. Plus, the welds are as strong as the plastic itself, so they last in tough jobs like medical tools. You don’t need to clean the parts much either, which saves even more time. Explore cost-saving ideas at our efficiency posts.
Works with All Plastics and Eco-Friendly
Whether it’s soft, hard, or super-tough plastic, vibration welding can handle it. It’s great for big, weird-shaped parts and doesn’t need much power, so it’s kind to the planet. It also makes airtight seals, like for water-tight containers. See how it stacks up at our comparison pages.
Product Spotlight: Our vibration welding machines are built for speed and precision!

Vibration Welding Machine
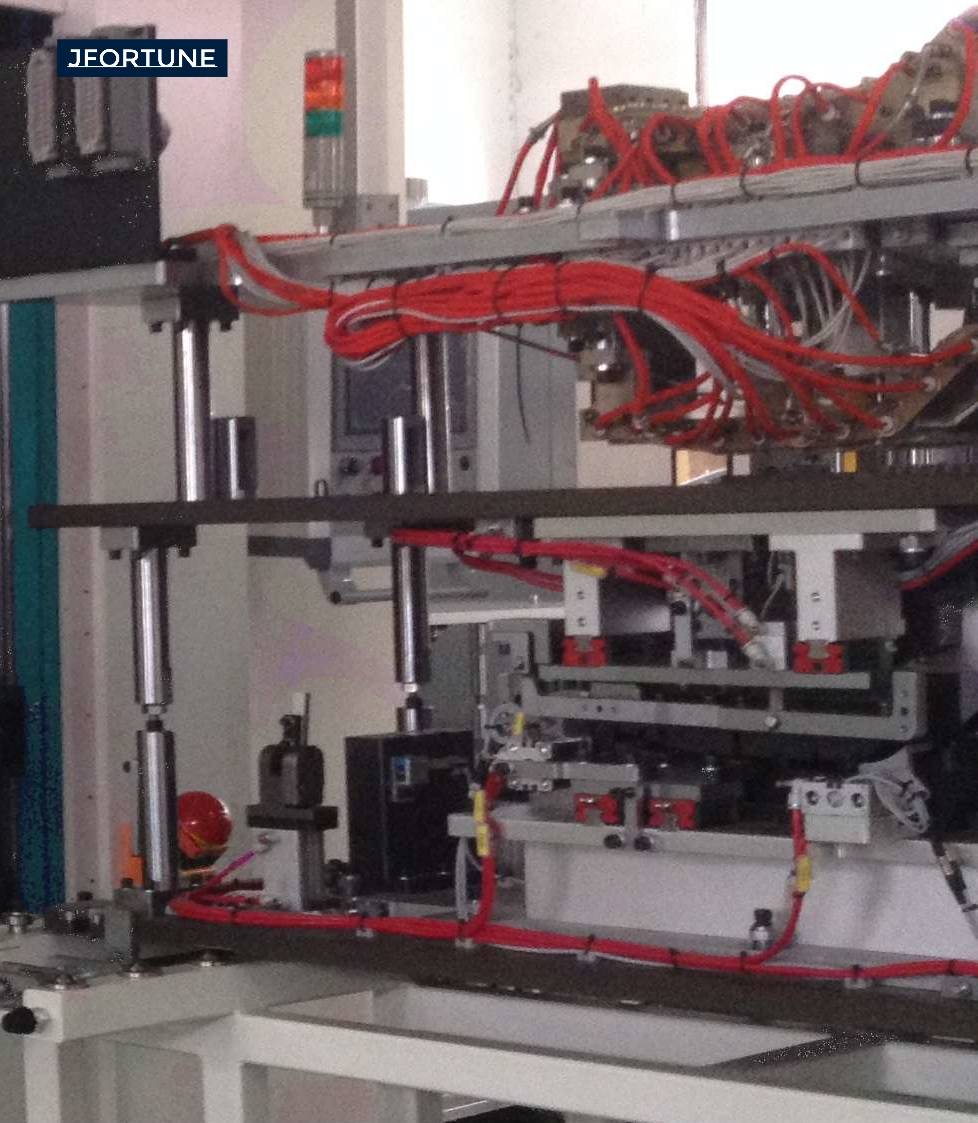
Hot Plate Welding Machine
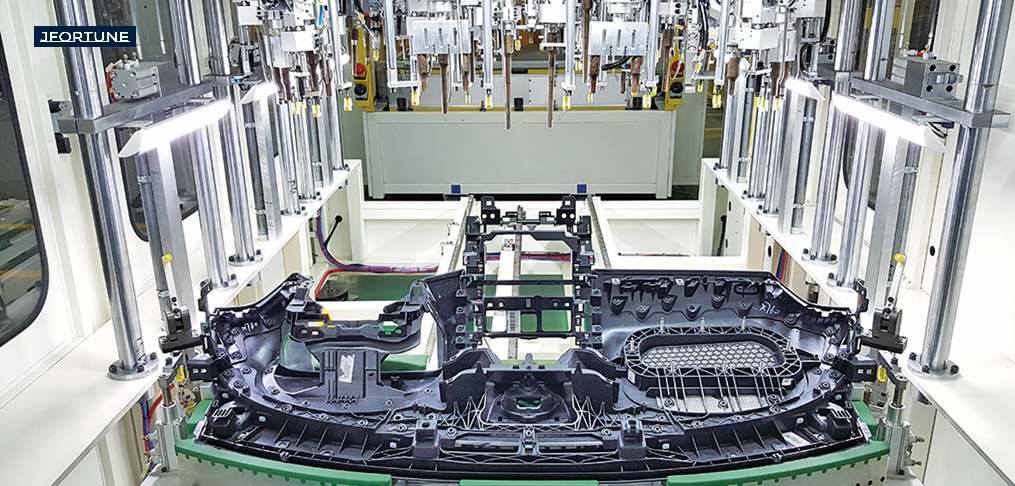
Ultrasonic Welding Machine
These machines make perfect welds every time. Browse more at our product categories.
How Vibration Welding Works
Vibration welding is like a science experiment that works every time. It uses friction to melt plastic and join parts together. Let’s walk through the steps to see how it’s done and why it’s so reliable for factories.
Step-by-Step Process
Here’s how it happens:
- Clamping: Two plastic parts are held tightly together with special tools.
- Vibrating: One part shakes super fast (100-240 Hz) against the other, making heat from friction.
- Holding: The shaking stops, and the melted plastic cools to form a solid bond.
- Separating: The finished part pops out, ready to use!
Why It’s So Precise
The machines control everything—pressure, speed, and time—so every weld is perfect. This is great for parts that need to fit exactly, like car dashboards. “Precision is why vibration welding dominates in automotive,” says Dr. Emily Chen from TechWeld Innovations. It works best for flat or slightly curvy surfaces, making it super versatile. Learn about machine specs at our equipment pages.
Perfect for Big Jobs
Unlike some methods, vibration welding can handle huge parts, like air ducts in cars. It’s fast and doesn’t need much setup, so factories can keep running smoothly. Plus, it works with all kinds of plastics, even ones with extra strength. Want to see it in action? Visit our case study blogs.
Vibration Welding vs. Other Methods
Not all plastic welding is the same. Vibration welding has some cool tricks that make it better than other methods like ultrasonic or hot plate welding. Let’s compare them to see why it’s a winner.
How It Stacks Up
Here’s a quick look at how vibration welding compares:
Метод | Best For | Why Vibration Wins |
---|---|---|
Ultrasonic Welding | Small, precise parts | Better for big parts, lower frequency. |
Hot Plate Welding | Flat, simple parts | Faster, less warpage issues. |
Infrared Welding | Thin, clear parts | Works with thick or opaque plastics. |
Why Vibration Welding is Better
Ultrasonic welding uses super high frequencies (20,000 Hz) and is great for tiny parts, but it struggles with big ones. Vibration welding uses lower frequencies (100-240 Hz) and can handle large, complex shapes. Hot plate welding is slower and can mess up if parts aren’t perfectly flat. Vibration welding fixes that with strong clamping. Infrared welding doesn’t work well with thick plastics, but vibration welding doesn’t care about thickness. “It’s the most flexible method for big parts,” says Mark Lee from WeldTech Solutions. Check out our method breakdowns.
When to Choose It
Pick vibration welding for big, tough jobs like car fuel tanks or appliance parts. It’s faster, stronger, and works with more plastics than other methods. Plus, it’s eco-friendly because it uses less energy. Want to compare machines? Visit our expert reviews.
Common Applications
Vibration welding is everywhere! It’s used in lots of industries to make strong, reliable products. Let’s check out where it’s making a difference.
Automotive Industry
Cars rely on vibration welding for parts like:
- Fuel tanks
- Headlights and taillights
- Air ducts
Appliances and Medical Devices
In appliances, it’s used for dishwasher pumps and soap dispensers. In medical devices, it makes airtight seals for sterile tools. “The hermetic seals are a game-changer for medical manufacturing,” says Dr. Sarah Kim from MediTech. Check out applications at our sector guides.
Packaging and Electronics
It seals leak-proof containers and joins parts in electronics, like phone cases. It’s fast and precise, perfect for these industries. Learn more at our product uses.
Real-World Success Stories
Vibration welding isn’t just talk—it’s proven in real factories. Here are some cool examples of how it’s helped.
Appliance Maker’s Big Win
A company making dishwashers switched from hot plate welding to vibration welding for pump housings. The result? They worked faster, saved energy, and got stronger, better-looking seals. This cut costs and made customers happy. Read more at our success stories.
Automotive Excellence
Car makers like BMW use our vibration welding machines for fuel tanks. The welds are so strong they pass tough safety tests, and the process is quick enough for big production lines. “Suzhou Jfortune’s machines are top-notch for automotive,” says Tom Brown from AutoTech. See more at our case studies.
Why It Works
These stories show vibration welding’s power: speed, strength, and reliability. At Suzhou Jfortune, we’ve helped brands like Audi and Jaguar with our machines. Want to join them? Check our client results.
Future Trends in Vibration Welding
Vibration welding is getting even cooler with new tech. Here’s what’s coming next.
Robots and Smart Tech
Factories are adding robots to make welding even faster and more precise. Smart sensors watch the process and fix problems instantly. “Automation is the future of welding,” says Lisa Wong from TechFuture. Learn about innovations at our tech blogs.
Smaller Machines, Bigger Markets
New compact machines fit smaller factories, and the market is growing, especially in Asia-Pacific. This means more companies can use vibration welding. See market trends at our industry updates.
New Plastics
Better plastics are coming, making welds even stronger. This opens doors for new products in cars and medical fields. Stay updated at our material news.
Why Choose Vibration Welding?
Vibration welding is a no-brainer for manufacturers. It’s fast, cheap, and makes super-strong, airtight seals. Plus, it works with big, tricky parts and all kinds of plastics.
Why It’s Smart
It saves time with quick welds and no cleanup. It saves money by skipping extra materials. And it’s reliable for tough jobs like car parts or medical tools. For more benefits, visit our advantage guides.
Why Suzhou Jfortune?
At Suzhou Jfortune, we’ve been perfecting welding machines since 2011, serving giants like BMW. Our machines are customizable, CE-certified, and backed by 24/7 support. Check our offerings at our product pages.
People Also Ask: Common Questions
Got questions? Here are answers to what people often ask about vibration welding.
Top Questions Answered
- What is vibration welding? A fast way to join plastics by rubbing them to make heat.
- How fast is it? As quick as 20 seconds!
- Can it handle big parts? Yes, it’s awesome for large, complex shapes.
- How’s it different from ultrasonic welding? It uses lower frequencies, great for bigger items.
Key Data Points
Here’s a quick table with cool stats about vibration welding.
Metric | Подробности |
---|---|
Weld Time | As low as 20 seconds |
Equipment Life | 12-16 years |
Market Trend | Growing through 2029, especially in automotive |
Conclusion: Take the Next Step with Vibration Welding
Vibration welding is a superstar for manufacturers, offering speed, strength, and savings. Whether you’re building car parts, appliances, or medical devices, it’s a reliable choice that boosts your production line. At Сучжоу Jfortune Precision Machinery Co., Ltd, we’re here to help you harness this technology with our top-quality machines and expert support. Ready to transform your manufacturing? Contact us today to explore our vibration welding solutions and see how we’ve helped brands like Audi and Jaguar succeed!
External Links for Further Reading: