- Vibration Welding Machines: Technology, Applications, and Market Trends in 2025
- Introduction to Vibration Welding Machines
- Core Technology Behind Vibration Welding
- Applications of Vibration Welding Machines
- Market Growth and Innovations in 2025
- Top Manufacturers of Vibration Welding Machines
- Vibration Welding vs. Other Welding Technologies
- Choosing the Right Vibration Welding Machine
- Future Trends in Vibration Welding Technology
- Conclusion
Vibration Welding Machines: Technology, Applications, and Market Trends in 2025
Introduction to Vibration Welding Machines
What Are Vibration Welding Machines?
Vibration welding machines are advanced tools used to join thermoplastic materials through frictional heat generated by high-frequency oscillations. This technology, widely adopted in industries like automotive, aerospace, and consumer goods, offers a reliable and efficient method for creating strong, durable bonds without the need for adhesives or fasteners. As detailed in the sitemap from VibrationWelding.com, these machines have evolved significantly, with innovations enhancing their precision and versatility.
The process involves clamping two plastic parts together and subjecting them to controlled vibrational forces, typically in the range of 100-240 Hz. The friction at the interface melts the material, and upon cooling, a solid weld forms. This method is particularly effective for large or complex components, making it a cornerstone of modern manufacturing.
Importance in Modern Manufacturing
In 2025, vibration welding machines are more critical than ever due to the growing demand for lightweight, sustainable materials in manufacturing. Industries are shifting toward thermoplastics to reduce vehicle weight in automotive production or to create eco-friendly packaging in consumer goods. According to the JFortuneMachine.com sitemap, advancements in automation and clean welding technologies are driving this adoption.
“Vibration welding is a game-changer for manufacturers aiming to balance efficiency with environmental responsibility,” says Dr. Emily Chen, a materials science expert with over 20 years in the industry. “Its ability to produce high-strength joints without additional materials aligns perfectly with today’s sustainability goals.”
Evolution of the Technology
From its inception in the mid-20th century, vibration welding has progressed from basic linear systems to sophisticated setups incorporating servo motors and infrared pre-heating, as noted in posts like Infrared Clean Vibration Welding Machine. The integration of robotics and smart controls has further refined the process, enabling precise welds for intricate designs. This evolution underscores why vibration welding remains a preferred choice in 2025’s competitive manufacturing landscape.
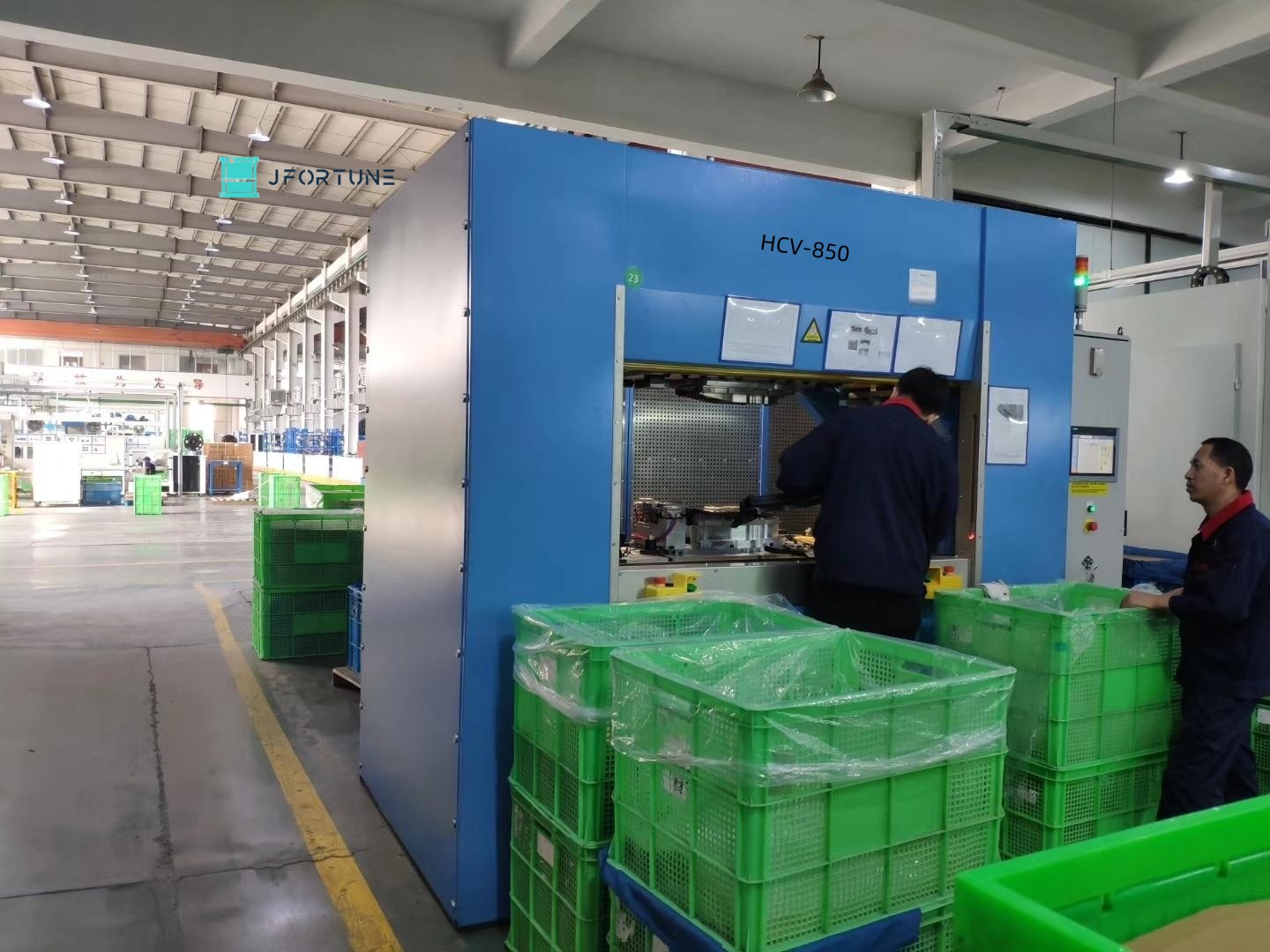
Branson Vibration Welding Machine
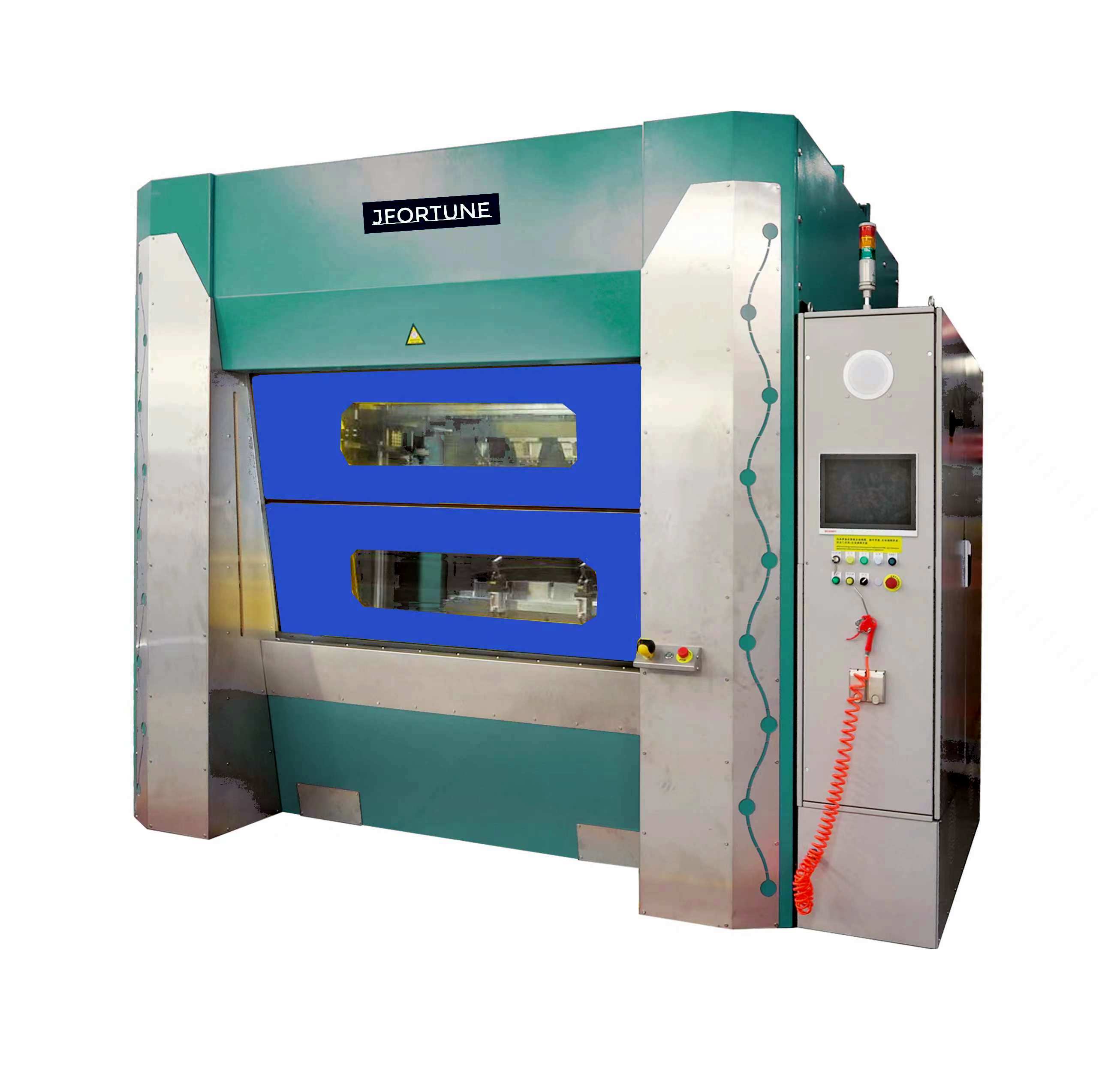
JFortune Vibration Welding Machine
Core Technology Behind Vibration Welding
How Vibration Welding Works
The core principle of vibration welding lies in converting mechanical energy into heat. Two parts are oscillated against each other at a specific frequency and amplitude, generating frictional heat that melts the contact surfaces. Once the vibration stops, the molten plastic solidifies under pressure, forming a robust weld. This process, detailed in Vibration Welding Machine Working Principle, is highly efficient for thermoplastics like polypropylene and nylon.
The technology’s simplicity belies its precision. Parameters such as frequency, amplitude, and pressure must be meticulously controlled to ensure optimal weld strength, making it suitable for applications requiring airtight seals or structural integrity.
Key Components of the Machine
A typical vibration welding machine comprises several critical components: the vibrating head (driven by an electromagnetic or hydraulic system), the fixture or tooling that holds the parts, and the control unit that manages the welding parameters. Advanced models, as seen in JFortune’s Vibration Welding Systems, may include servo motors for enhanced accuracy and infrared systems for pre-heating, reducing cycle times and improving weld quality.
“The tooling design is as crucial as the machine itself,” notes John Matthews, a senior engineer at a leading welding equipment firm. “Custom fixtures tailored to specific parts can significantly boost productivity and consistency.”
Advancements in Vibration Welding Technology
Recent advancements have propelled vibration welding into new realms of efficiency. The incorporation of infrared cleaning, as explored in Infrared Clean Vibration Welding, minimizes contaminants, ensuring cleaner welds. Additionally, automation and real-time monitoring systems allow for seamless integration into smart factories, aligning with Industry 4.0 trends and enhancing scalability in 2025.
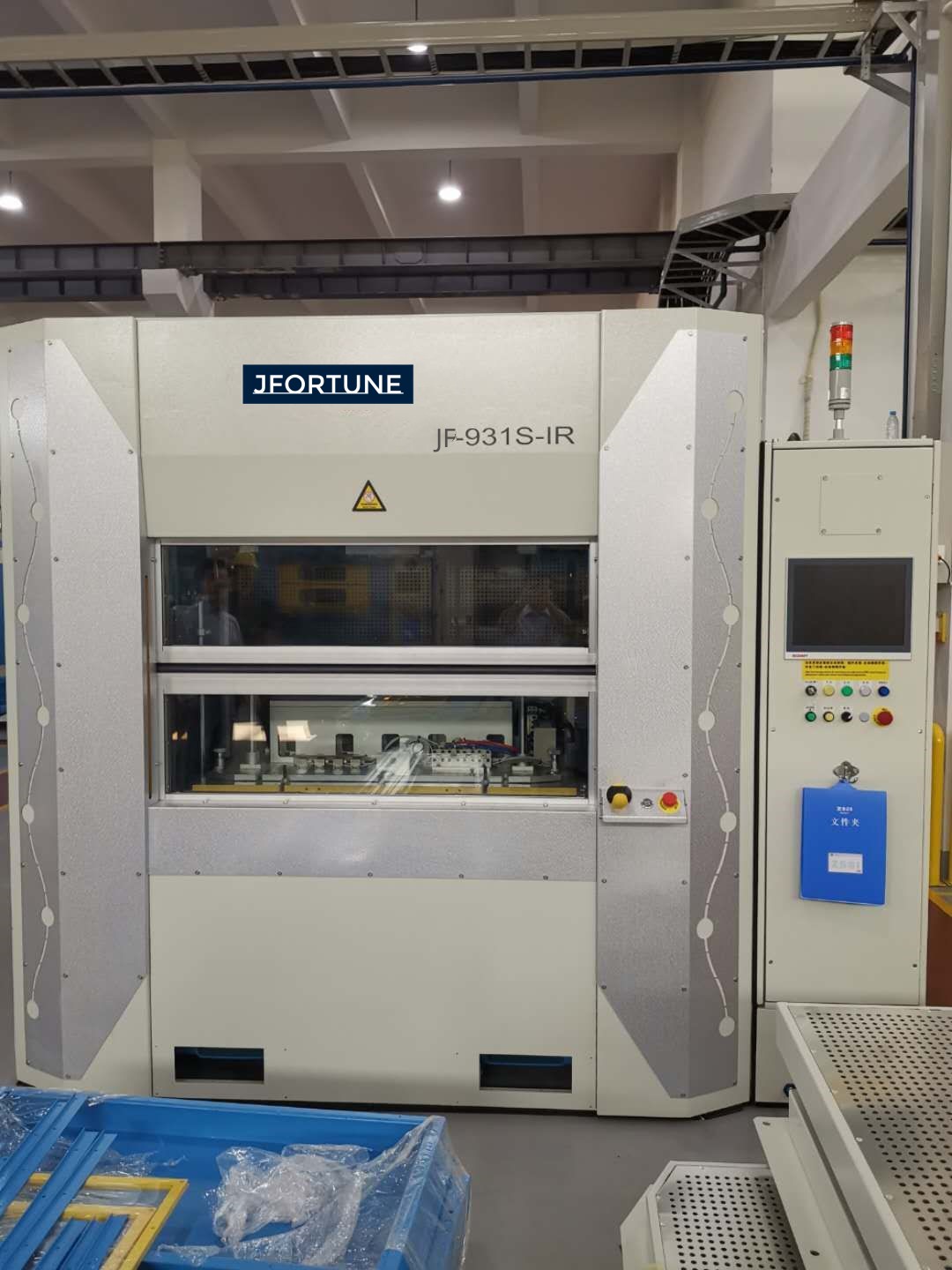
Infrared Cleaning Technology
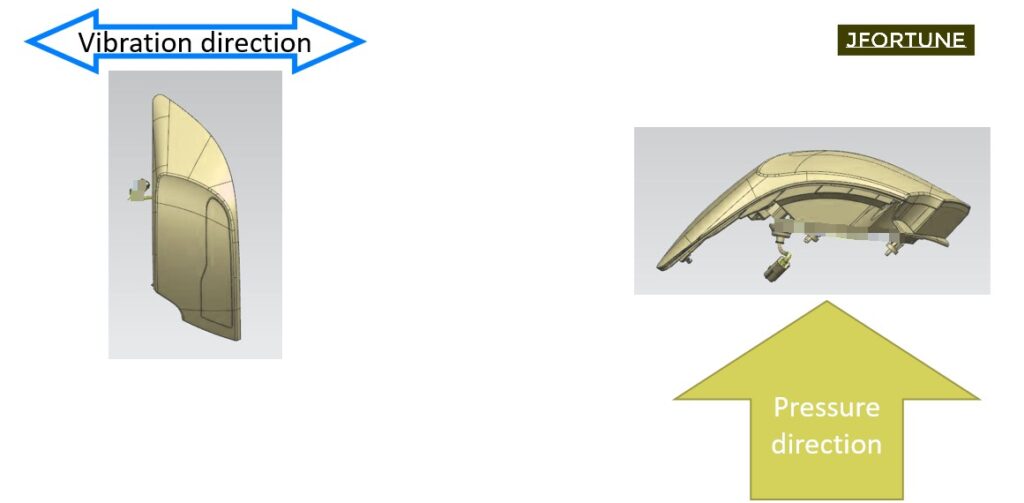
Advanced Vibration Welding System
Applications of Vibration Welding Machines
Automotive Industry Applications
Vibration welding machines are indispensable in the automotive sector, used for assembling components like intake manifolds, air ducts, and lighting systems. The Vibration Welding Machine for Automotive Lighting highlights their role in enhancing production precision. These machines enable manufacturers to join large, complex parts, reducing vehicle weight while maintaining structural integrity—a key focus in 2025 as electric vehicle production ramps up.
Consumer Goods and Electronics
Beyond automotive, vibration welding is pivotal in consumer goods and electronics, crafting items like appliance housings and battery casings. The technology’s ability to produce hermetic seals makes it ideal for products requiring durability and protection, as noted in JFortune’s Plastic Welding Machine overview. Its versatility supports the rapid production cycles demanded by these fast-moving markets.
Other Industrial Uses
Vibration welding extends to industries like packaging, where it’s used for pallet welding (Pallet Vibration Welder Automation), and medical device manufacturing, where precision and cleanliness are paramount. “The adaptability of vibration welding to various materials and shapes is unmatched,” says Dr. Chen. “It’s why we see it across such diverse applications in 2025.”
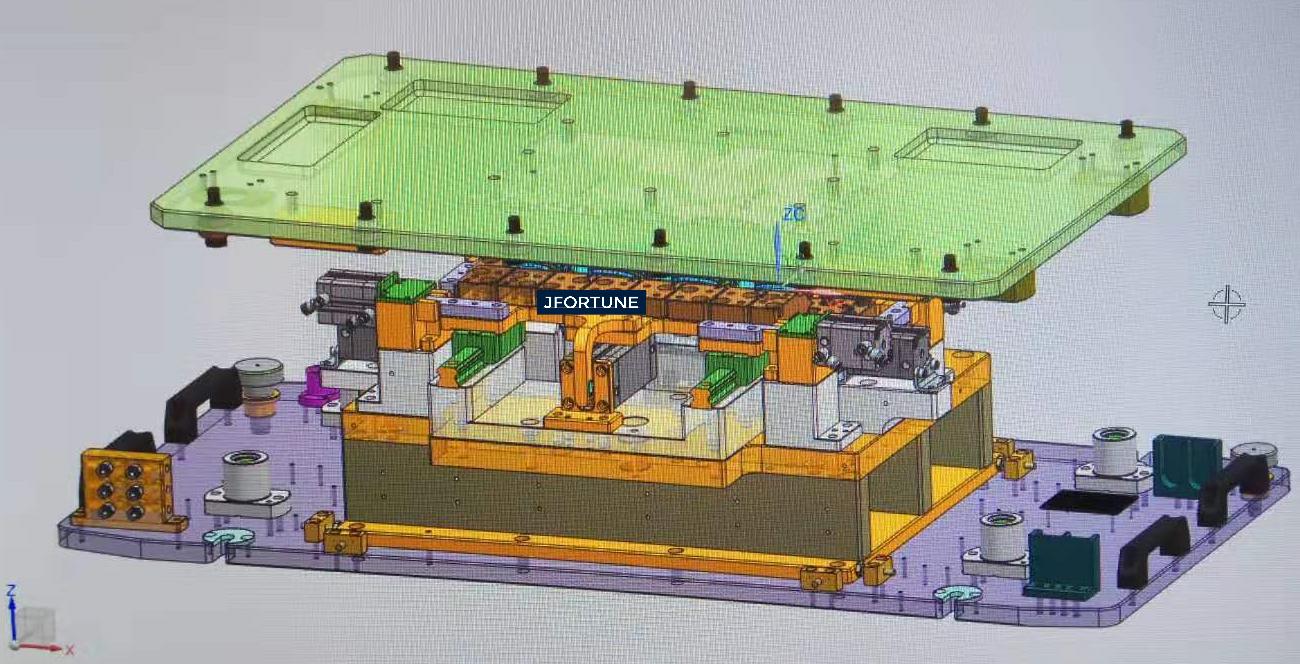
Intake Manifold Application
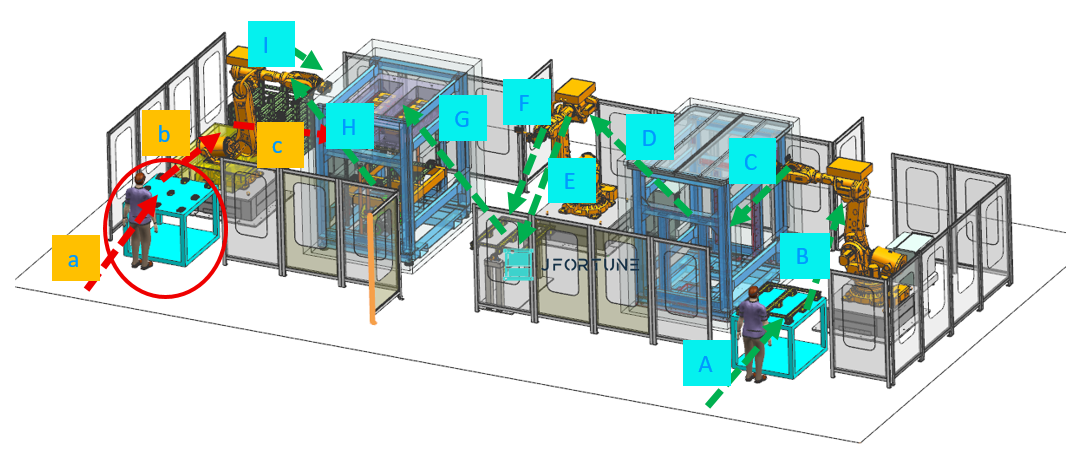
Pallet Welding Automation
Market Growth and Innovations in 2025
Current Market Size and Forecast
The vibration welding machine market is experiencing steady growth, largely due to the rising use of thermoplastics in industries like automotive and manufacturing. According to a detailed analysis on JFortuneMachine.com, the market is expected to achieve a compound annual growth rate (CAGR) of 5.8% from 2023 to 2030, reaching an estimated value of $1.2 billion by 2025. This surge is driven by the automotive industry’s push for lightweight materials and the global emphasis on sustainable production methods.
The Asia-Pacific region, especially China and India, is poised to dominate this growth. Manufacturers in these areas are ramping up investments in cutting-edge welding technologies to cater to both domestic and international markets. “The Asia-Pacific region is becoming a powerhouse for vibration welding advancements,” says industry expert Mark Thompson. “We’re witnessing an unprecedented increase in production capabilities and innovation.”
Technological Innovations
In 2025, vibration welding is evolving with groundbreaking advancements. The integration of artificial intelligence (AI) and machine learning is enhancing predictive maintenance and optimizing welding processes, as noted in Future Trends in Vibration Welding. These technologies minimize downtime and ensure consistent weld quality. Additionally, hybrid welding methods—combining vibration with ultrasonic or laser techniques—are broadening the technology’s applications.
Servo-driven systems are another key development, providing precise control over welding parameters. This results in improved accuracy and energy efficiency, making them ideal for high-volume production settings where reliability and speed are critical.
Impact of Industry 4.0
Industry 4.0 is revolutionizing vibration welding by introducing smart manufacturing practices. Internet of Things (IoT) and big data enable real-time performance monitoring through sensors and centralized systems. This allows for proactive maintenance, reducing defects and downtime. Remote diagnostics and software updates further enhance machine longevity and efficiency.
“Adopting Industry 4.0 isn’t just a passing fad—it’s essential for staying ahead,” explains Dr. Emily Chen, a manufacturing technology specialist. “Companies that integrate these smart systems will dominate the market in 2025 and beyond.”

Market Growth Projection

Industry 4.0 Enabled Machine
Top Manufacturers of Vibration Welding Machines
Leading Companies in the Market
The vibration welding machine market features several prominent players. Branson, part of Emerson, stands out with its high-performance equipment, such as the Branson Vibration Welding Machine. Known for its precision and durability, it’s a top choice for automotive manufacturing.
Dukane is another industry leader, excelling in versatile welding solutions for medical and packaging sectors. Their machines are user-friendly and adaptable, meeting the needs of manufacturers with varied production demands.
Emerging Players and Startups
Besides established giants, newer companies like JFortune Machine are gaining ground. Their offerings, detailed on the Vibration Welding Machine Manufacturer page, emphasize quality and customization. Startups are also emerging, targeting niche markets with specialized, innovative solutions that are increasingly popular.
“The market is primed for new players to shake things up,” says Mark Thompson. “These entrants are using advanced materials and digital tools to challenge traditional leaders.”
Comparative Analysis of Top Brands
Comparing leading brands reveals distinct strengths. Branson shines in high-volume production, Dukane offers flexibility for diverse operations, and JFortune excels in tailored solutions. Factors like reliability, support services, and innovation guide manufacturer choices, depending on specific production goals.
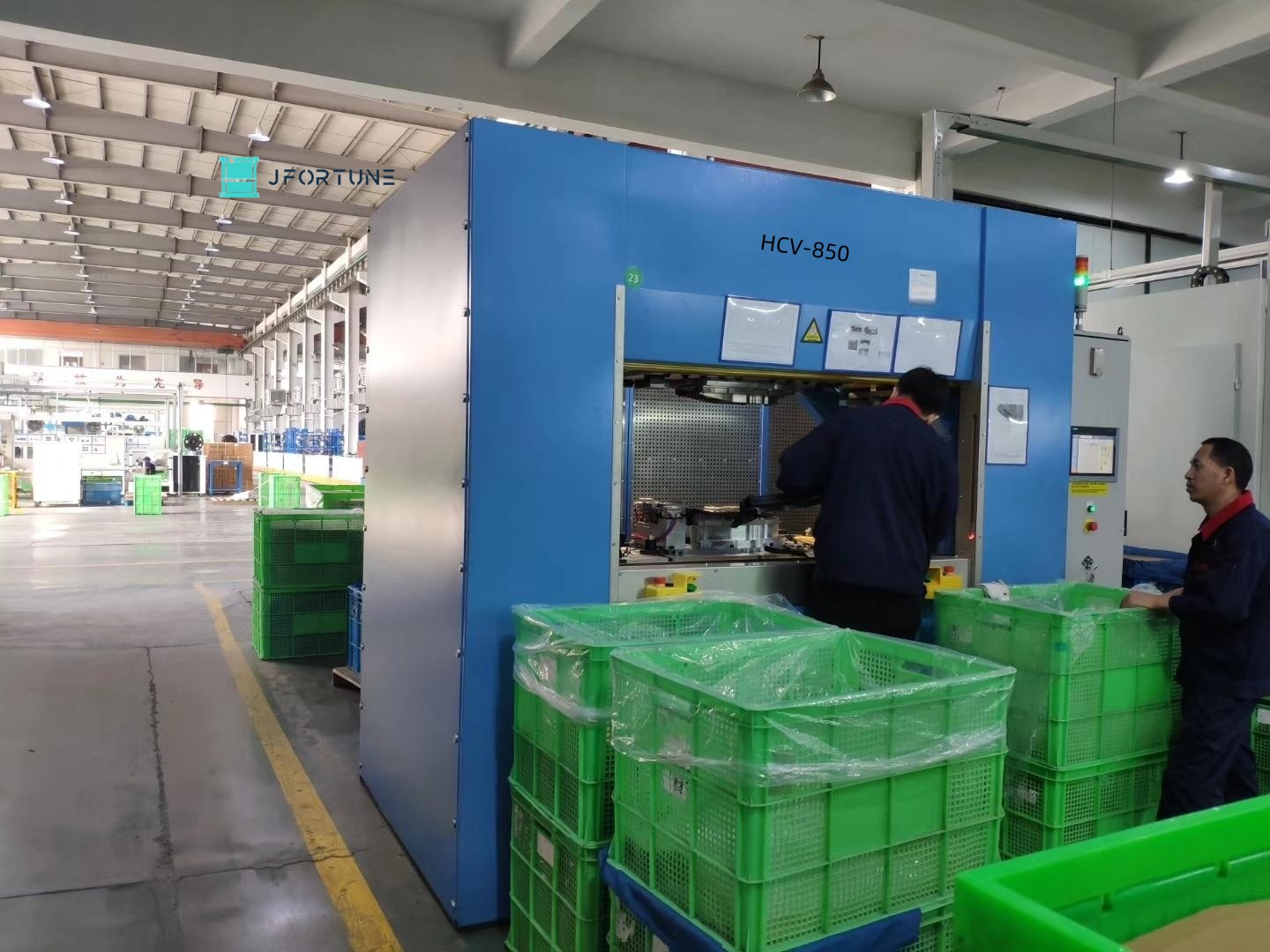
Branson Vibration Welder
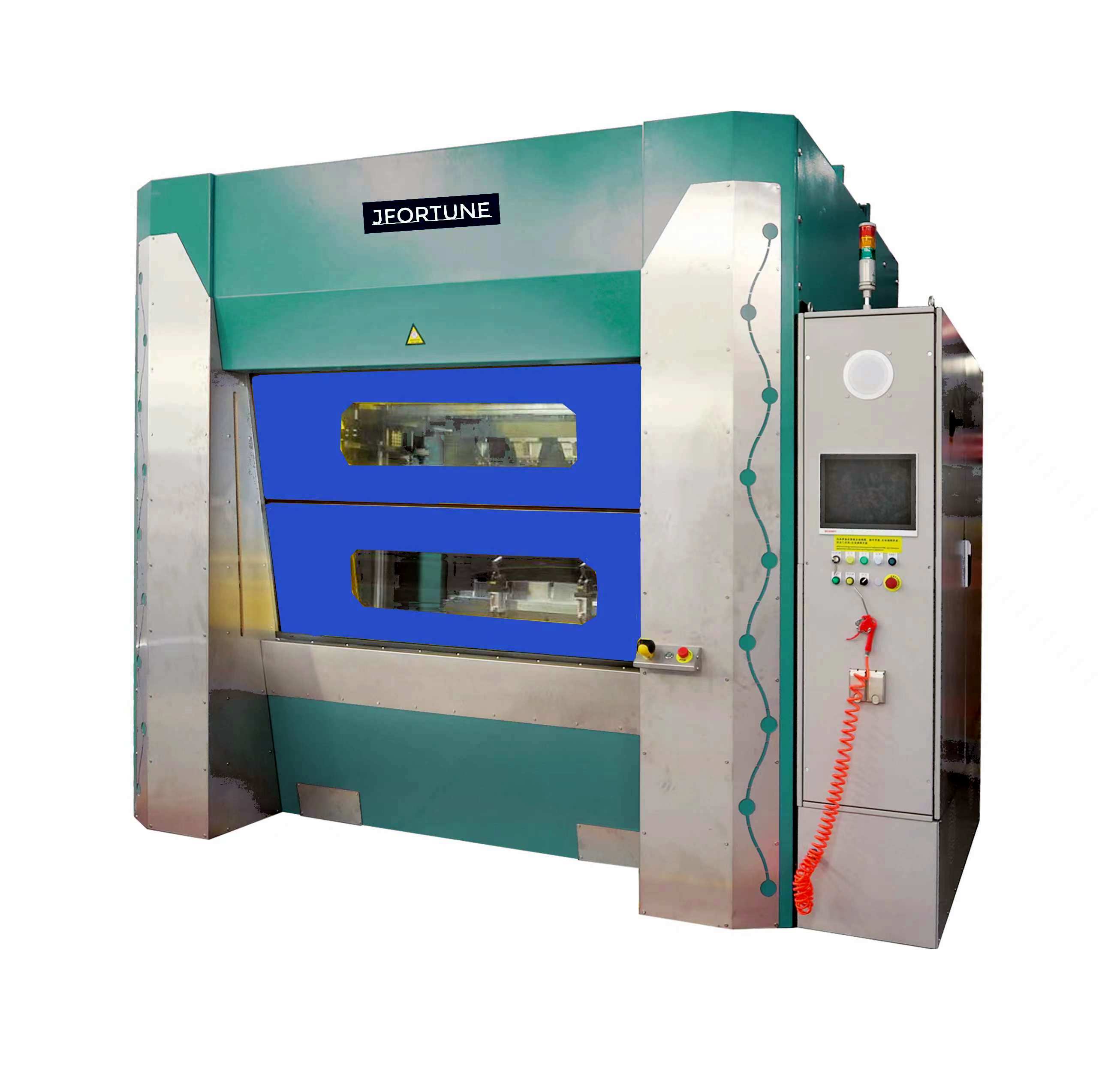
JFortune Vibration Welder
Vibration Welding vs. Other Welding Technologies
Comparison with Ultrasonic Welding
While both vibration and ultrasonic welding rely on frictional heat, their uses differ. Ultrasonic welding suits smaller, delicate parts, whereas vibration welding handles larger components effectively. The Vibration Welding vs. Ultrasonic Welding comparison highlights ultrasonic’s precision for small tasks and vibration’s strength for automotive applications.
Comparison with Hot Plate Welding
Hot plate welding heats parts directly before joining, contrasting with vibration welding’s frictional approach. Although effective, it’s slower and less efficient than vibration welding. The Hot Plate Welding Machine works well for simple shapes, but vibration welding excels with complex geometries and larger parts.
Advantages and Disadvantages
Vibration welding boasts high strength, minimal waste, and versatility with dissimilar materials. However, it requires precise setup and higher initial costs. Ultrasonic welding is cheaper and faster for small parts but less robust. Hot plate welding, while flexible, often leads to longer cycles and more waste.
“The best technology hinges on the job at hand,” advises John Matthews, a welding expert. “Vibration welding is unmatched for large, intricate parts, but ultrasonic fits smaller, precise needs better.”

Comparison of Welding Technologies

Hot Plate Welding Application
Choosing the Right Vibration Welding Machine
Factors to Consider
Selecting the ideal vibration welding machine involves evaluating several key factors. First, consider the material type and part size, as different machines are optimized for specific thermoplastics and dimensions. The required weld strength and cycle time are also crucial—high-volume production demands faster machines, while precision applications may prioritize accuracy over speed.
Budget constraints and available floor space should not be overlooked. Some machines offer modular designs for flexibility, while others are more compact but less versatile. The Vibration Welding Machine Selection Guide provides a comprehensive overview of these considerations.
Customization and Scalability
Customization is increasingly important in 2025, with manufacturers offering tailored solutions for unique production needs. Machines with adjustable parameters and interchangeable tooling can adapt to various part designs, enhancing scalability. “Investing in a machine that grows with your business is smart,” advises John Matthews. “Look for systems that can be upgraded or expanded as production demands evolve.”
Maintenance and Support
Reliable maintenance and support are essential for minimizing downtime. Choose manufacturers with strong service networks and readily available spare parts. Machines with built-in diagnostics and remote monitoring capabilities can preemptively address issues, ensuring smooth operations. The Vibration Welding Machine Maintenance guide offers best practices for keeping equipment in top condition.

Customized Welding Solution

Maintenance Best Practices
Future Trends in Vibration Welding Technology
Predictions for 2025 and Beyond
The future of vibration welding looks promising, with several trends poised to shape the industry. Automation will continue to advance, with fully autonomous welding cells becoming more common. These systems will integrate seamlessly with other manufacturing processes, reducing human intervention and increasing efficiency.
Sustainability will also drive innovation, with a focus on energy-efficient machines and recyclable materials. “The industry is moving towards greener solutions,” notes Dr. Emily Chen. “Expect to see machines that consume less power and produce minimal waste.”
Emerging Applications
New applications for vibration welding are emerging, particularly in the renewable energy sector. The technology is being explored for assembling components in wind turbines and solar panels, where durability and precision are paramount. Additionally, the medical industry is adopting vibration welding for sterile, high-strength joints in devices and packaging.
Sustainability and Green Manufacturing
As environmental concerns grow, vibration welding’s ability to join recyclable thermoplastics without adhesives positions it as a sustainable choice. Manufacturers are increasingly adopting closed-loop systems that recycle scrap material, further reducing waste. The Sustainable Vibration Welding Practices article delves deeper into these eco-friendly initiatives.

Emerging Welding Technologies

Sustainable Welding Practices
Conclusion
Vibration welding machines have become indispensable in modern manufacturing, offering unparalleled strength, efficiency, and versatility. As industries evolve, these machines will continue to adapt, driven by technological advancements and sustainability goals. Whether you’re in automotive, consumer goods, or emerging sectors, understanding and leveraging vibration welding technology is key to staying competitive in 2025 and beyond.
For more insights and updates on vibration welding, visit VibrationWelding.com and JFortuneMachine.com.